Onze procesdeskundigheid maakt het onmogelijke mogelijk
Het snijvlak is altijd daar waar niet veel mensen de weg kennen. Als je de producten van morgen wilt maken, moet je de noodzakelijke processen vandaag beheersen – en dat is precies wat RUCH NOVAPLAST doet. Als technologieleider in de verwerking van partikelschuimen hebben we het onze missie gemaakt om innovatieve oplossingen met de hoogste precisie te realiseren.
Bij RUCH NOVAPLAST kunt u erop vertrouwen dat wij ons te allen tijde op uw eisen zullen richten.
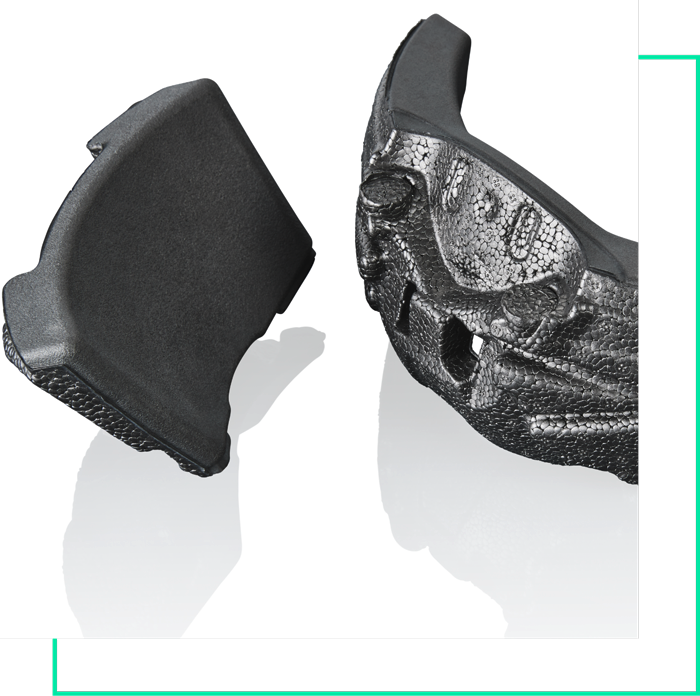
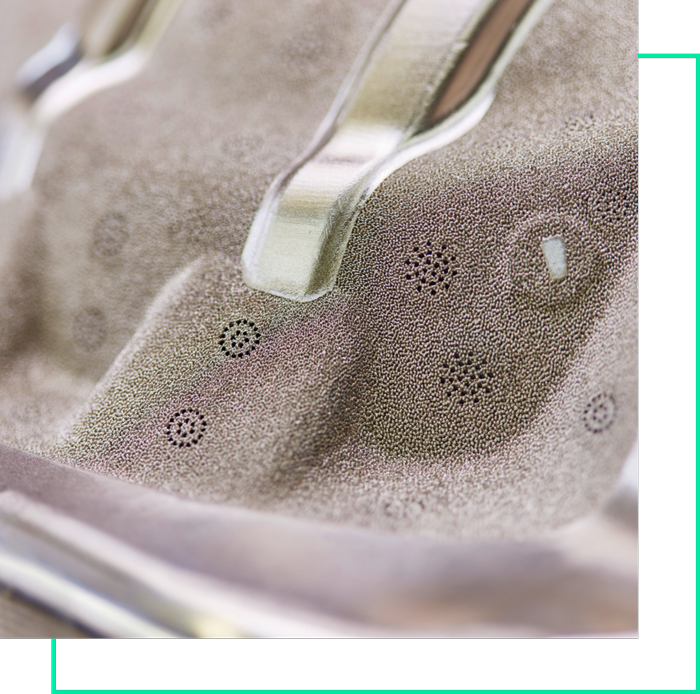
Baanbrekende, speciaal ontwikkelde processen
Met behulp van ultramoderne processen zoals thermisch verbinden en het gebruik van hoogontwikkelde spuitgietgereedschappen produceren we duurzame, functionele spuitgietonderdelen die u een duidelijk concurrentievoordeel geven. Veel van deze processen hebben we zelf ontwikkeld: van energie-geoptimaliseerde productie met High Efficiency Tools (H.E.T.) en gelijktijdig schuimen van verschillende dichtheden (dubbele dichtheid) of materialen (2-componenten componenten) tot innovatief composiet spuitgieten van partikelschuim (PVSG).
Door RUCH NOVAPLAST zelf ontwikkelde processen en patenten
Met onze procesdeskundigheid creëren we op maat gemaakte, efficiënte en toekomstbestendige producten – perfect afgestemd op uw eisen. Onze eigen processen en gepatenteerde technologieën vormen onze basis als technologieleider. In dit gedeelte stellen we ze in detail aan u voor – en leggen we uit hoe ze uw producten nog efficiënter en krachtiger maken.
Het opschuimen van componenten maakt de naadloze integratie van mechanische inzetstukken of elektronische componenten zoals printplaten rechtstreeks in het spuitgietproduct mogelijk. Tijdens het opschuimen worden de inzetstukken precies opgeschuimd of omgespoten, waardoor een materiaal- of vormvaste verbinding ontstaat. Dit proces biedt niet alleen mechanische stabiliteit, maar maakt het ook mogelijk om te voldoen aan vereisten zoals elektromagnetische compatibiliteit (EMC), wat vooral belangrijk is voor behuizingssystemen met gevoelige elektronica.
Het opschuimen van decors combineert thermovormen en opschuimen in één productiestap en een gemeenschappelijke opschuimmal. Een thermoplastische, thermovormbare film – bijvoorbeeld van lak, metaal, TPO of andere materialen – wordt in het schuimproces teruggeschuimd. Deze technologie maakt de productie van hygiënische oppervlakken van hoge kwaliteit mogelijk. Bovendien kunnen CF/KF laminaten, roosters of structuren naadloos met partikelschuim worden verbonden met behulp van bindmiddelen. Dit resulteert in lichtgewicht sandwichcomponenten die ondanks hun lage gewicht een hoge mechanische belastbaarheid hebben. Dit proces opent een brede waaier aan mogelijkheden voor decoratieve en technische toepassingen in de lichtgewichtbouw.
Het dual-density proces maakt het mogelijk om verschillende hardheidsgraden in een vormdeel te bereiken in één enkele productiestap. Door de vulgebieden binnen de matrijsholte specifiek te scheiden, kunnen materialen met verschillende dichtheden tegelijkertijd worden opgeschuimd en gecombineerd met een precieze pasvorm. Een typisch voorbeeld is het gebruik in herbruikbare verpakkingen: het buitenste gedeelte wordt geproduceerd met een hogere dichtheid (bv. 80 g/l) voor maximale stabiliteit, terwijl de binnenste holtes gemaakt worden van een zachter materiaal (bv. 30 g/l). Dit beschermt gevoelige onderdelen tegen stoten en krassen. Dubbele dichtheid biedt ook duidelijke voordelen op het gebied van schokbescherming: Verschillende materiaaldichtheden optimaliseren het impactgedrag.
Dunwandige technologie maakt de precieze productie mogelijk van onderdelen met een wanddikte van minder dan 3 mm, waardoor we filigrane geometrieën kunnen realiseren. Dankzij de optimale combinatie van materiaalselectie, matrijsontwerp en procescontrole maken we de reproduceerbare productie van dunwandige producten van geëxpandeerd polypropyleen (EPP) mogelijk. Deze technologie breidt de gebruiksmogelijkheden van EPP uit en maakt het aantrekkelijk voor toepassingen die voorheen niet overwogen werden vanwege de vereiste materiaaldikte.
De High Efficiency Tool (H.E.T.) is een interne ontwikkeling die het energieverbruik bij de productie van spuitgietproducten aanzienlijk vermindert. Afhankelijk van de toepassing kunnen we met H.E.T. gereedschap 35 tot 47% energie besparen. Deze energieoptimalisatie vermindert niet alleen de koolstofvoetafdruk van het eindproduct, maar heeft ook een positief effect op de kostprijs. Om de potentiële besparingen nauwkeurig te bepalen, raden we aan om vooraf een productspecifieke CO₂-berekening uit te voeren.
Het kiezen van de juiste combinatie van materialen is cruciaal voor een betrouwbaar verlijmingsproces. Afhankelijk van de gebruikte materialen en de mechanische eisen van de verbinding wordt de juiste lijm geselecteerd. We baseren dit op uitgebreide ervaring en uitgebreide tests en analyses. Na de selectie zorgt ons gedeeltelijk geautomatiseerde verlijmingsproces, ondersteund door cobots, voor een consistente, nauwkeurige uitvoering van het proces en garandeert het een constant hoge kwaliteit van de gelijmde verbindingen. Zo bereiken we betrouwbare en efficiënte resultaten voor serieproductie.
Bij composiet spuitgieten van partikelschuim (PVSG) vormen partikelschuimkorrels een unieke en onlosmakelijke materiaalverbinding met kunststofgranulaten (spuitgieten), die zelfs bij hoge belasting intact blijft. Met deze technologie kunnen de voordelen van partikelschuim zoals EPP of EPS worden gecombineerd met de positieve eigenschappen van thermoplasten zoals ABS, PP of TPE om functionele lichtgewicht onderdelen te maken. Het resultaat zijn stabiele artikelen met een laag gewicht, krachtabsorberende componenten met een haptisch aantrekkelijk oppervlak, thermisch isolerende producten met geïntegreerde bevestigings- en houdfuncties, eenvoudig te installeren behuizingen of isolerende lichtgewicht componenten met een verhoogde stijfheid. PVSG vormt de basis voor de productie van onze NOVAfeed&fix® serie.
PUR lamineren biedt een hoogwaardig, aanpasbaar oppervlak dat we in bijna elke kleur en zelfs met glas- of koolstofversterkingen kunnen produceren. In een tweede verwerkingsstap wordt het geschuimde partikelschuimdeel in een PUR mal geplaatst en gedeeltelijk of volledig onder water gezet. De resulterende coating van het gevormde onderdeel kan dus aan één of alle zijden worden geproduceerd en is extreem robuust. Het proces is klaar voor serieproductie en is geschikt voor onderdelen tot een grootte van 2000 mm.
Skinning is een efficiënte afwerkingstechniek die oppervlakken van partikelschuim glad en robuust maakt zonder spuitmonden. Door het eenzijdig elektrisch temperen van de schuimvormholtes smelt het oppervlak van het vormdeel, waardoor de korrels vloeibaar worden en een geplastificeerde coating vormen. Het resultaat is een slijtvast, slijtvast oppervlak dat doet denken aan spuitgieten. RUCH NOVAPLAST gebruikt dit proces om stabiele serieonderdelen in grote hoeveelheden te produceren met behoud van de gunstige eigenschappen van EPP, zoals isolerende eigenschappen en veerkracht. Het proces wordt met succes gebruikt bij de productie van kindelen voor motorhelmen en onderdelen voor luchtverdeling.
Voor toepassingen op het gebied van hoofd- en lichaamsbescherming
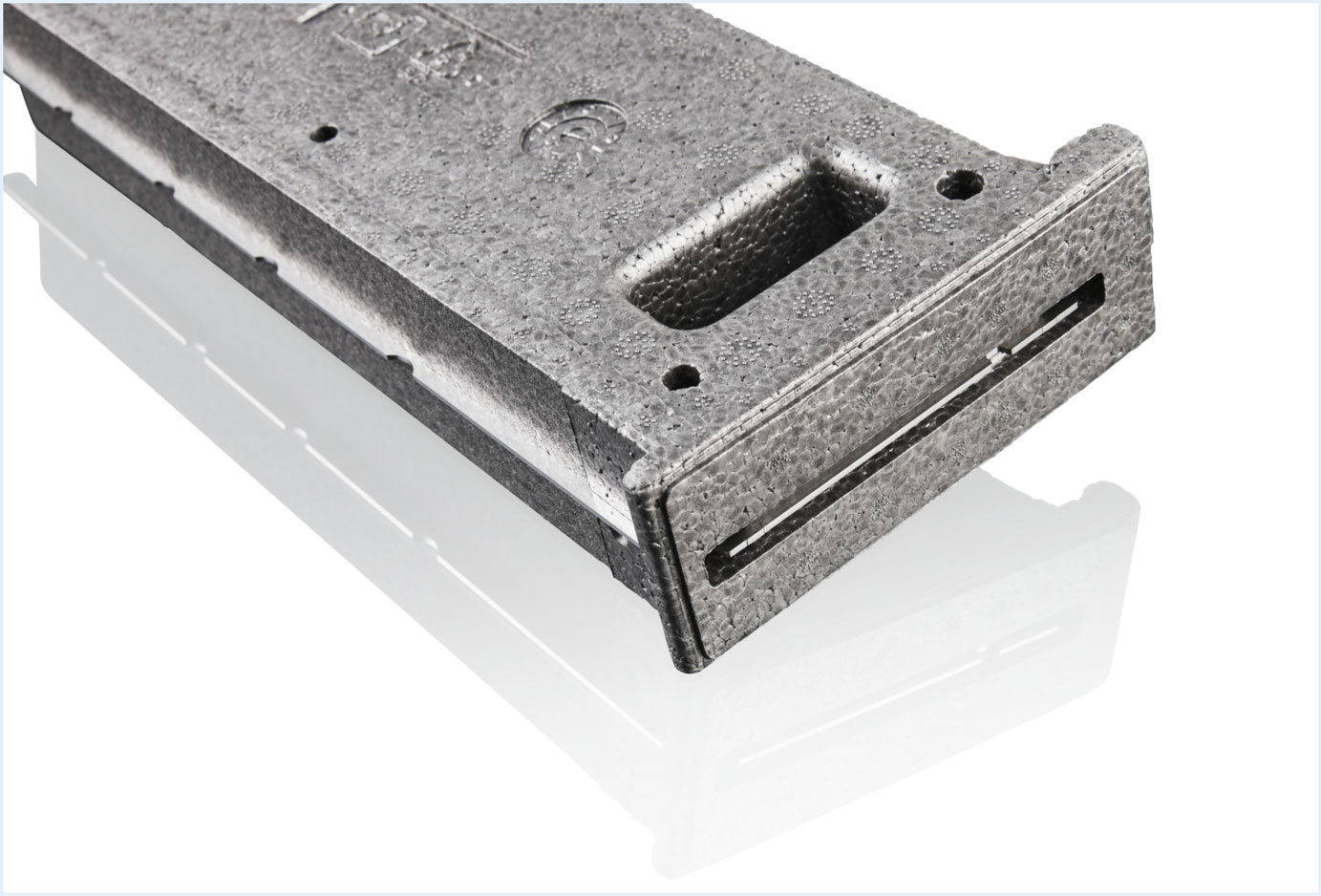
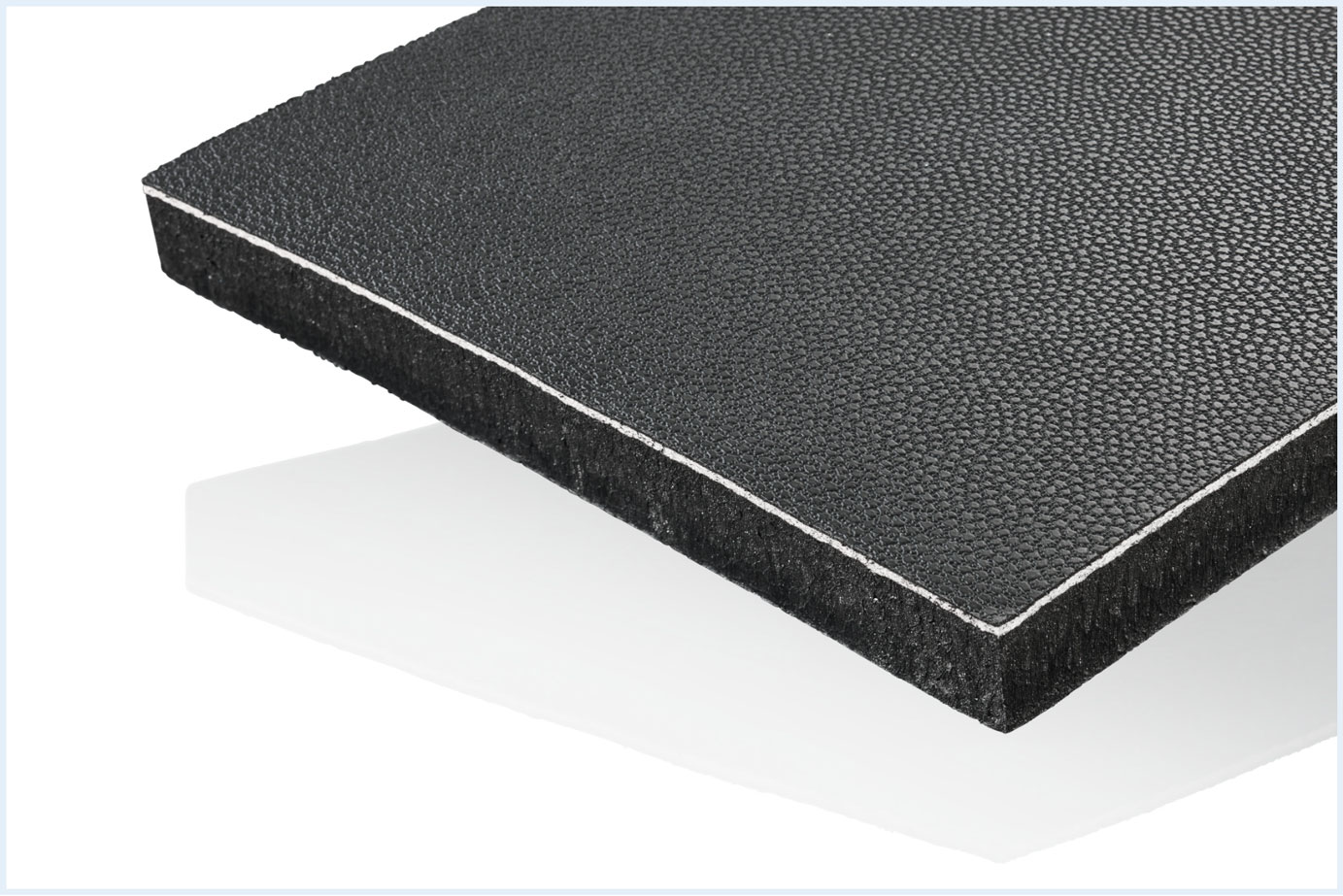
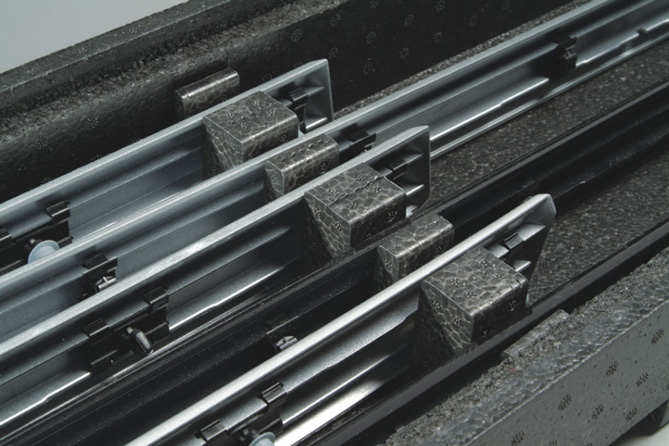
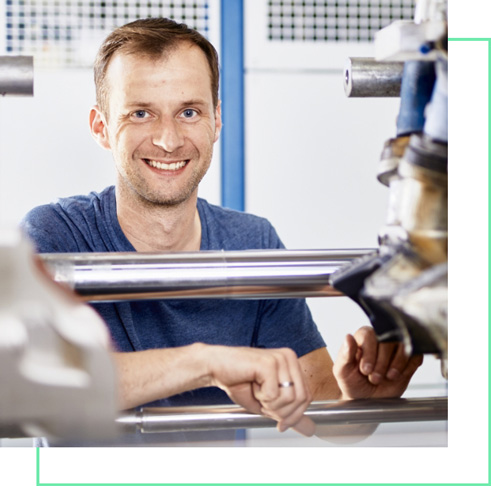
Baanbrekende producten vereisen innovatieve processen die hun productie überhaupt mogelijk maken. Met onze expertise in partikelschuim creëren we unieke mogelijkheden voor onze klanten. We zijn er trots op onze klanten te ondersteunen, een revolutie in de industrie teweeg te brengen en nieuwe normen te stellen.