Joining molded parts: material bonding and sustainable
RUCH NOVAPLAST specializes, among other things, in joining moulded parts to form a system. After all, joining technology is of central importance in almost all applications. When selecting the connection, we focus entirely on your requirements: Should the connection be detachable or not? What forces act on the system? Are there additional requirements for tightness? These questions need to be clarified before we decide on a connection technology.
With Snap-Lock technology, we create a stable connection that can be released again. We achieve this by equipping the two components with a tongue and groove connection – it acts like a clip fastener and snaps together. The bonding also makes it possible to achieve an inseparable joining between two or more molded parts made of the same or different materials.
Another technology is NOVAweld®. This is a ground-breaking technology for the material-bonded joining of molded particle foam parts.
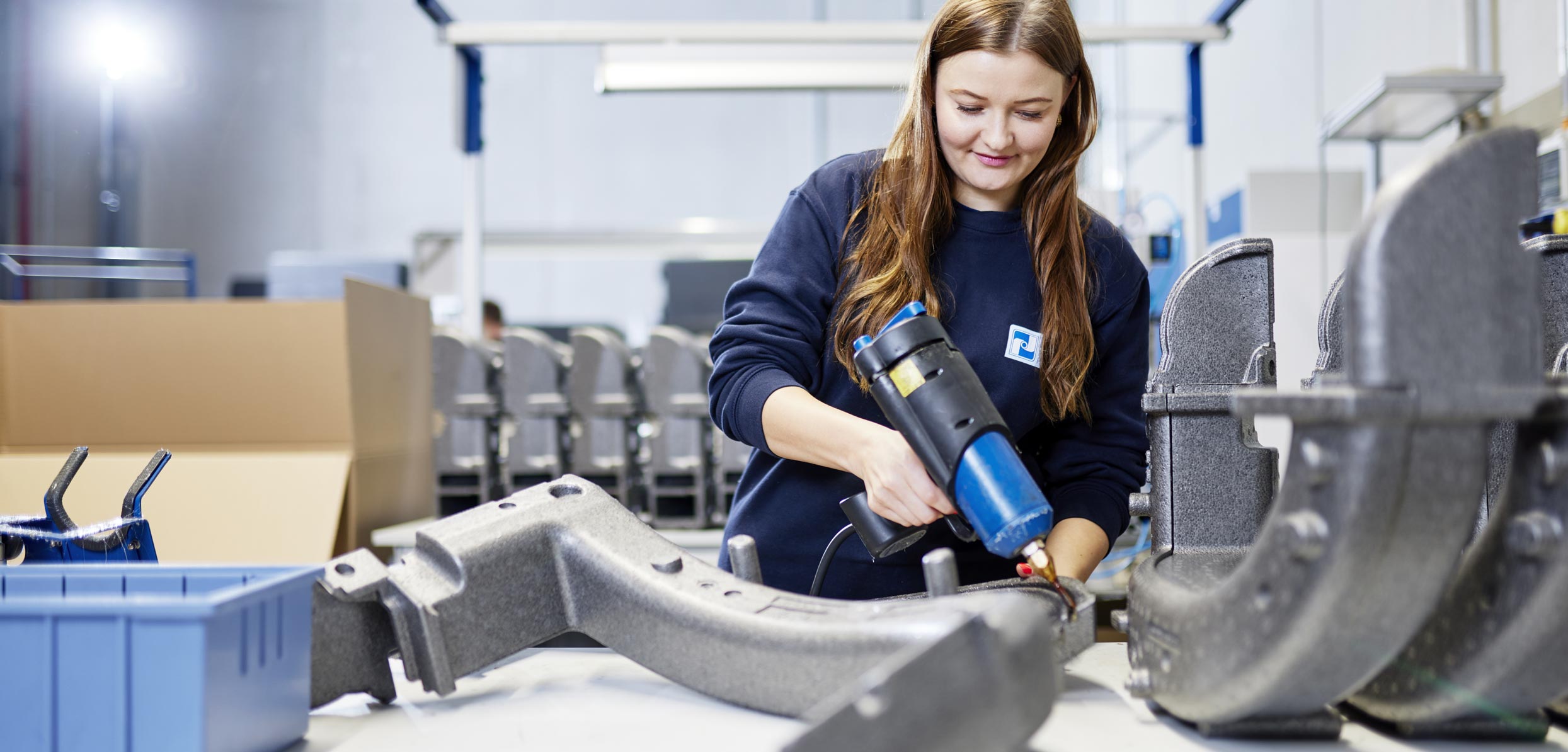
NOVAweld® enables material-bonded joining of molded parts
We call our process NOVAweld®, a method that creates a strong, material-bonded joining between plastic components. This results in secure and stable compositions, as well as geometries and part sizes that would otherwise be impossible to manufacture. By using this technique, we can significantly reduce the complexity of individual molded parts as well as the complexity of the foam molding tools themselves.
Joining molded parts has a number of advantages, especially in the HVAC sector
NOVAweld® technology enables the thermal joining of molded parts to form a material bond that provides ideal insulation and airtightness – particularly important for complex systems such as in the HVAC sector. The specific material properties are retained.
Another highlight is the thermal joining of particle foam molded parts including inserts. They are inserted into the parting line before joining, positioned and then joined together. In this way, we integrate the inserts into the assembly.