Our process expertise makes the impossible possible
The cutting edge is always where not many people know their way around. If you want to manufacture the products of tomorrow, you have to master the necessary processes today – and RUCH NOVAPLAST does just that. As a technology leader in the processing of particle foams, we have made it our mission to implement innovative solutions with the highest precision.
At RUCH NOVAPLAST, you can rely on us to focus on your requirements at all times.
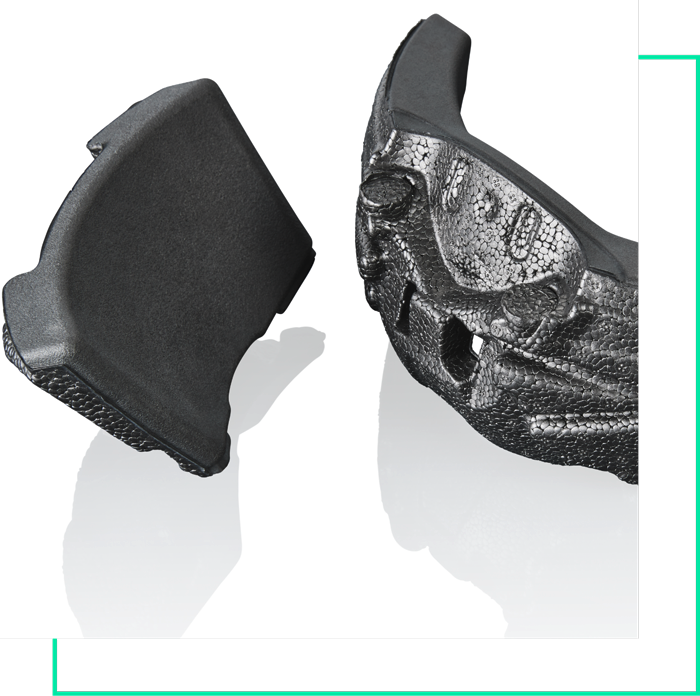
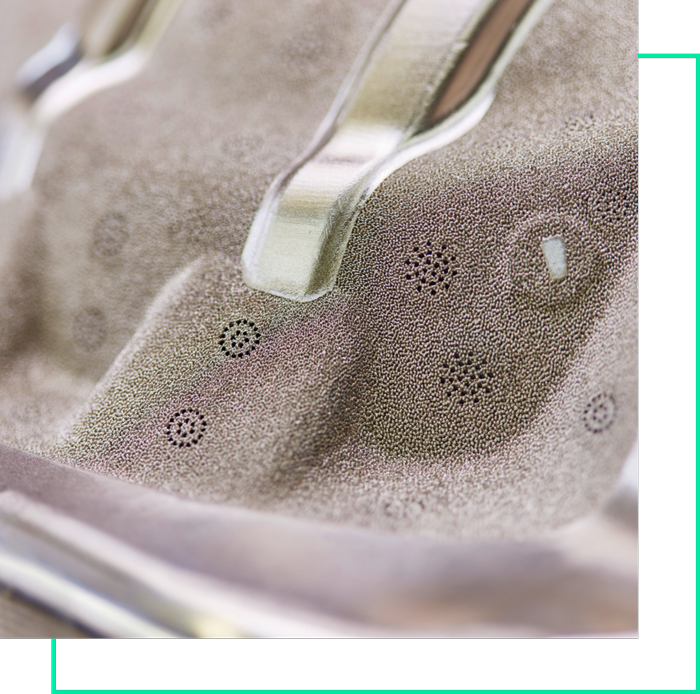
Pioneering, specially developed processes
Using state-of-the-art processes such as thermal joining and the use of highly developed molding tools, we create durable, functional molded parts that give you a clear competitive advantage. We have developed many of these processes ourselves: from energy-optimized production with High Efficiency Tools (H.E.T.) and simultaneous foaming of different densities (dual density) or materials (2-component components) to innovative particle foam composite injection moulding (PVSG).
Processes and patents developed in-house by RUCH NOVAPLAST
With our process expertise, we create custom-fit, efficient and future-proof products – perfectly tailored to your requirements. Our proprietary processes and patented technologies are our foundation as a technology leader. In this section, we present them to you in detail – and explain how they make your products even more efficient and powerful.
Foaming-in of components enables the seamless integration of mechanical inserts or electronic components such as circuit boards directly into the molded part. During the foaming process, the inserts are precisely foamed in or encapsulated in foam, creating a material or form-fit connection. This process not only offers mechanical stability, it also makes it possible to meet requirements such as electromagnetic compatibility (EMC), which is particularly important for enclosure systems with sensitive electronics.
The back-foaming of decors combines thermoforming and back foaming in a single production step and a common foaming tool. A thermoplastic, thermoformable film – made of lacquer, metal, TPO or other materials, for example – is back-foamed in the foaming process. This technology enables the production of high-quality, hygienic surfaces. In addition, CF/KF laminates, grids or structures can be seamlessly combined with particle foam using adhesion promoters. This creates lightweight sandwich elements that have a high mechanical load-bearing capacity despite their low weight. This process opens up a wide range of possibilities for decorative and technical applications in lightweight construction.
The dual-density process makes it possible to realize different degrees of hardness within a moulded part in a single production step. By specifically separating the filling areas within the mold cavity, materials with different densities can be foamed at the same time and combined with a precise fit. A typical example is the use in reusable containers: the outer area is produced with a higher density (e.g. 80 g/l) for maximum stability, while the inner cavities are made of a softer material (e.g. 30 g/l). This protects sensitive components against impact and scratches. Dual density also offers clear advantages in terms of impact protection: Different material densities optimize the impact behaviour.
Thin-wall technology enables the precise production of components with wall thicknesses of less than 3 mm, allowing us to realize filigree geometries. Through the optimal combination of material selection, tool design and process control, we enable the reproducible production of thin-walled products made of expanded polypropylene (EPP). This technology expands the possible uses of EPP and makes it attractive for applications that were previously not considered due to the required material thickness.
The High Efficiency Tool (H.E.T.) is an in-house development that significantly reduces energy consumption in the production of molded parts. Depending on the application, we can achieve savings of 35 to 47% of the energy used with H.E.T. tools. This energy optimization not only reduces the CO₂ footprint of the end product, but also has a positive effect on the cost price. To precisely determine the potential savings, we recommend a product-specific CO₂ calculation in advance.
Choosing the right combination of materials is crucial for a reliable bonding process. The right adhesive is selected depending on the materials used and the mechanical requirements of the joint. We base this on extensive experience as well as comprehensive tests and evaluations. After selection, our partially automated bonding process, supported by cobots, ensures consistent, precise execution of the process and guarantees the consistently high quality of the bonded joints. This is how we achieve reliable and efficient results for series production.
In particle foam composite injection molding (PVSG), particle foam beads form a unique and inseparable material bond with plastic granules (injection molding), which remains intact even under high loads. This technology allows the advantages of particle foams such as EPP or EPS to be combined with the positive properties of thermoplastics such as ABS, PP or TPE to create functional lightweight components. The results are strong products with low weight, force-absorbing components with a haptically appealing surface, thermally insulating products with integrated fixing and retaining functions, easy-to-install housings or insulating lightweight components with increased rigidity. PVSG forms the basis for the production of our NOVAfeed&fix® series.
PUR lamination offers a high-quality, customizable surface that we can produce in almost any color and even with glass or carbon reinforcements. In a second processing step, the foamed particle foam part is inserted into a PUR mold and partially or completely flooded. The resulting coating of the molded part can therefore be produced on one or all sides and is extremely robust. The process is ready for series production and is suitable for components up to a size of 2,000 mm.
Skinning is an efficient finishing technique that makes particle foam surfaces smooth and robust without nozzles. By electrically tempering the foaming tool cavities on one side, the surface of the molded part is melted, causing the granules to liquefy and form a plasticized coating. The result is a durable, abrasion-resistant surface that has a certain similarity to injection moulding. RUCH NOVAPLAST uses this process to produce stable series parts in large quantities while retaining the advantageous properties of EPP, such as insulating properties and resilience. The process is used successfully in the production of chin parts for motorcycle helmets and air distribution components.
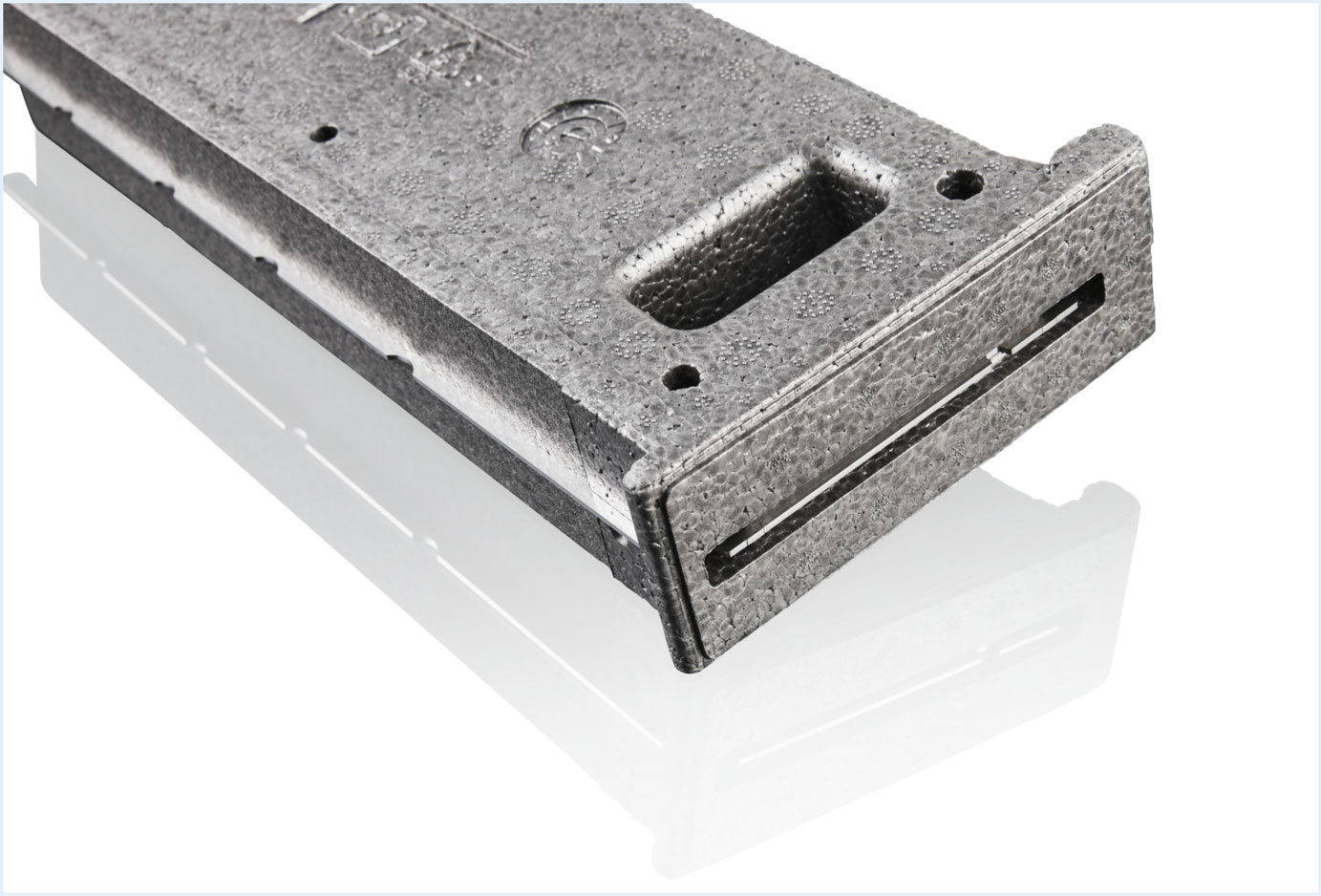
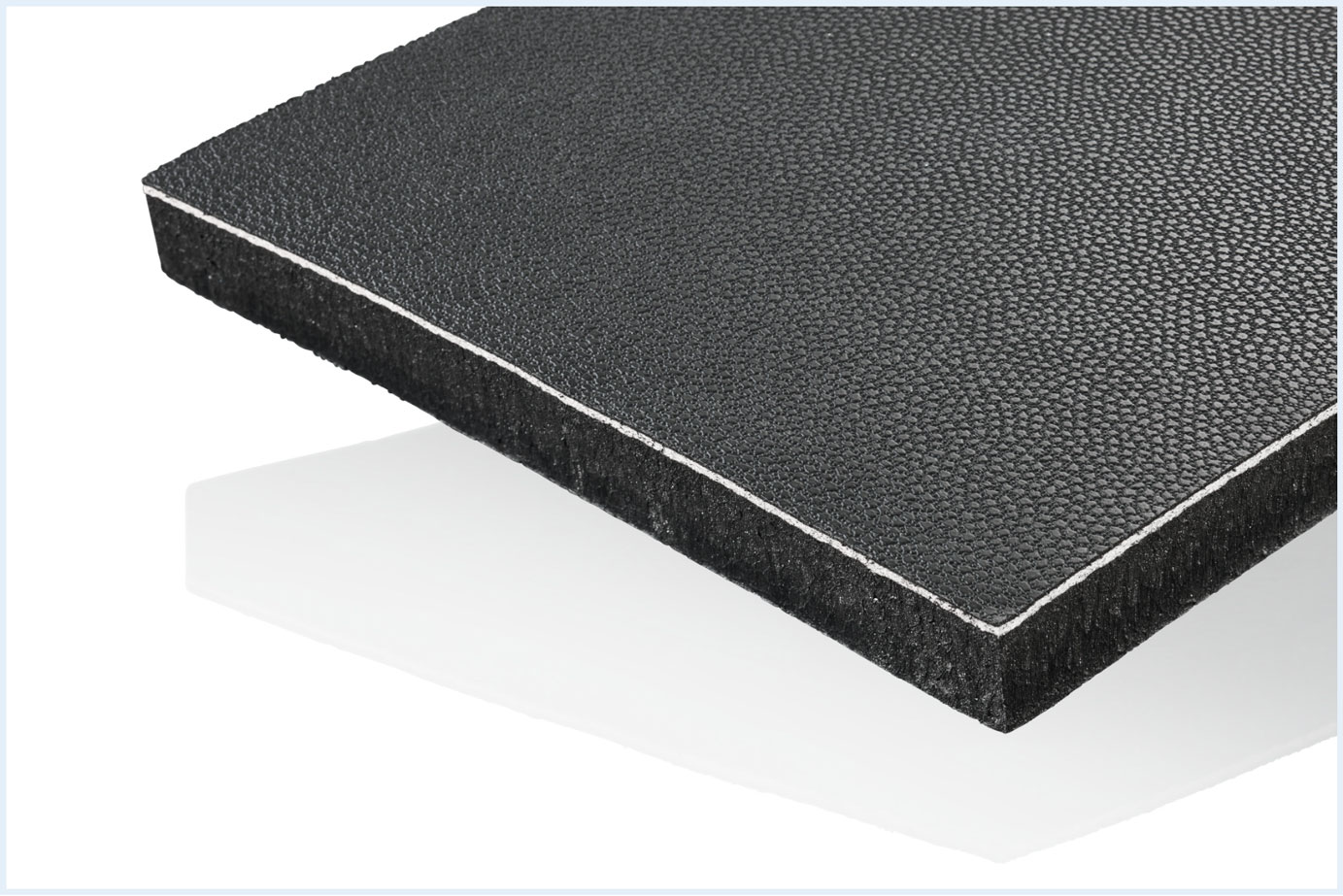
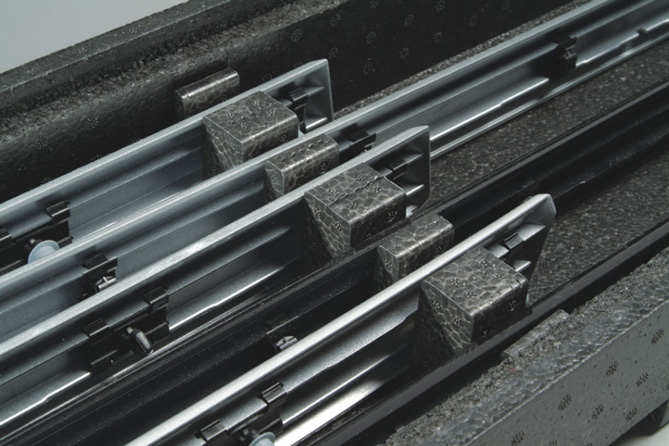
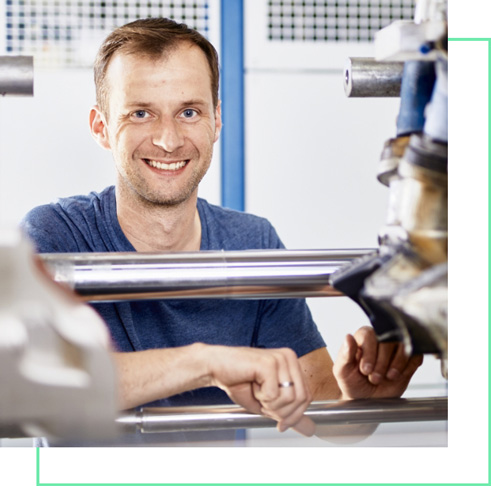
Pioneering products require innovative processes that make their manufacture possible in the first place. With our expertise in particle foams, we create unique opportunities for our customers. We are proud to support our customers, revolutionize the industry and set new standards.